ISH Trade Fair: A New Chapter
and Kospel’s 35th Anniversary
The ISH trade fair serves as an inspiration for Kospel to present our brand in a refreshed and modernized form. As a leading manufacturer of heating systems, we are proud to actively participate in the remarkable transformation of our industry. We feel a great responsibility to provide solutions that are both economically accessible to a wide range of customers and environmentally sustainable. The ISH theme, “Solutions for a Sustainable Future”, perfectly reflects our mission and values.
Since the last in-person ISH event, the Kospel team has been hard at work refining our brand and offerings. Our products are designed to last for many years, ensuring safe and comfortable climates in homes. ISH is the perfect platform to showcase our forward-thinking technologies, and we are excited to introduce several innovations.
This year, we will present our heat pumps for domestic hot water at the trade fair. The range includes wall-mounted models with capacities from 80 to 150 liters and floor-standing models with capacities from 250 to 300 liters. These devices are characterized by high efficiency, exceptionally low energy consumption, and the use of environmentally friendly refrigerants, making them an excellent choice for modern homes.
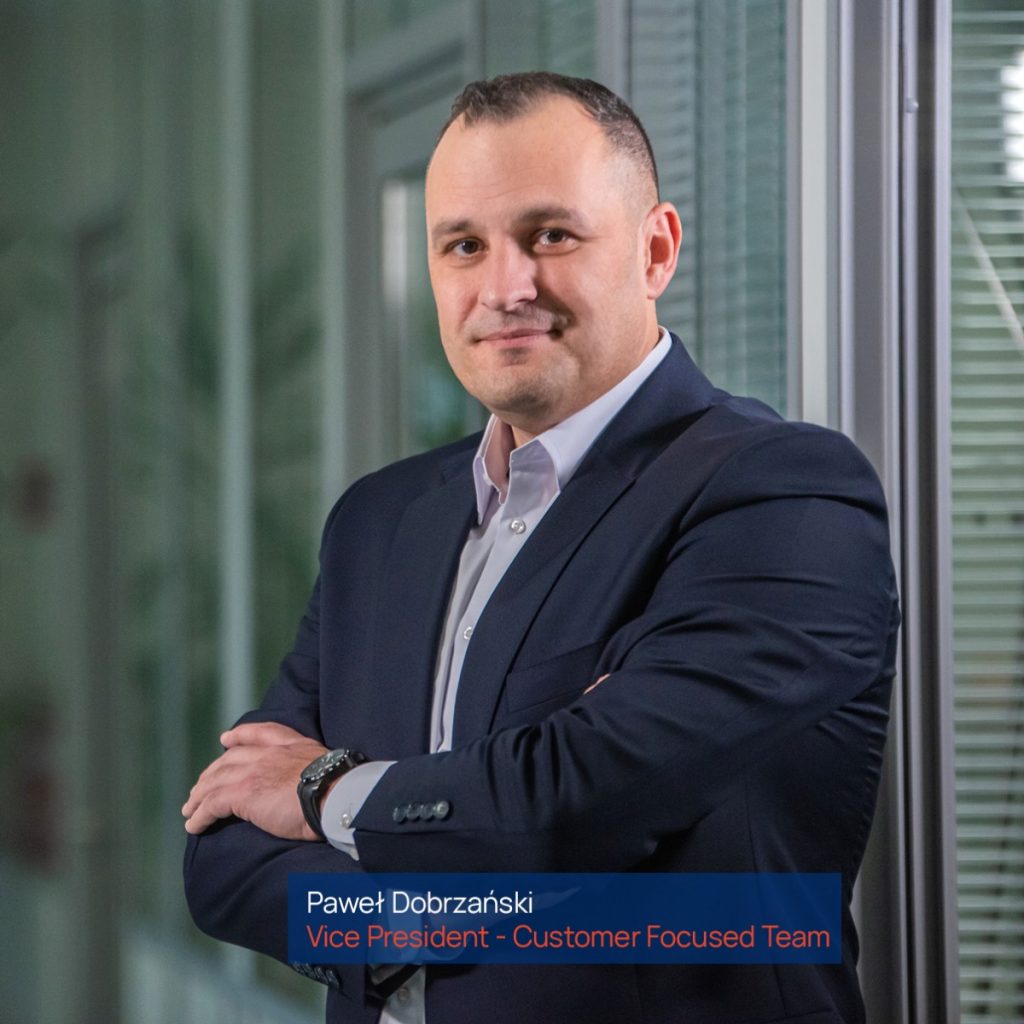
During this year’s ISH, we will also inaugurate the celebration of Kospel’s 35th anniversary. As part of this milestone, we will showcase the interior of our new, state-of-the-art factory for domestic hot water heat pumps and unveil a new product line in this segment.
We look forward to welcoming you to the ISH platform from March 17th to 21st, 2025, where we will share knowledge, experiences, and inspirations that shape the future of heating systems. Visit us in Hall 12.0, Booth E79
Welcome to the Future
Building Europe's Most Advanced Domestic Hot Water Exchanger FactoryWe proudly and excitedly present our latest initiative – the new Kospel factory.
This ambitious project aims to launch the most advanced factory in Europe, specializing in the production of domestic hot water cylinders. The new production hall, with an impressive area of 13,000 m², will be equipped with advanced, automated production and auxiliary processes that will elevate our production capabilities to a whole new level.
Coil Production – Revolution in Automation
The automated production line at BoWiD2 will fully automatically produce coils necessary for manufacturing our cylinders. Our modern technologies include plasma welding, rolling, threading, calibration, and surface preparation of the coil through washing in an integrated production line washer. This process not only enhances efficiency but also precision and quality of the final product.
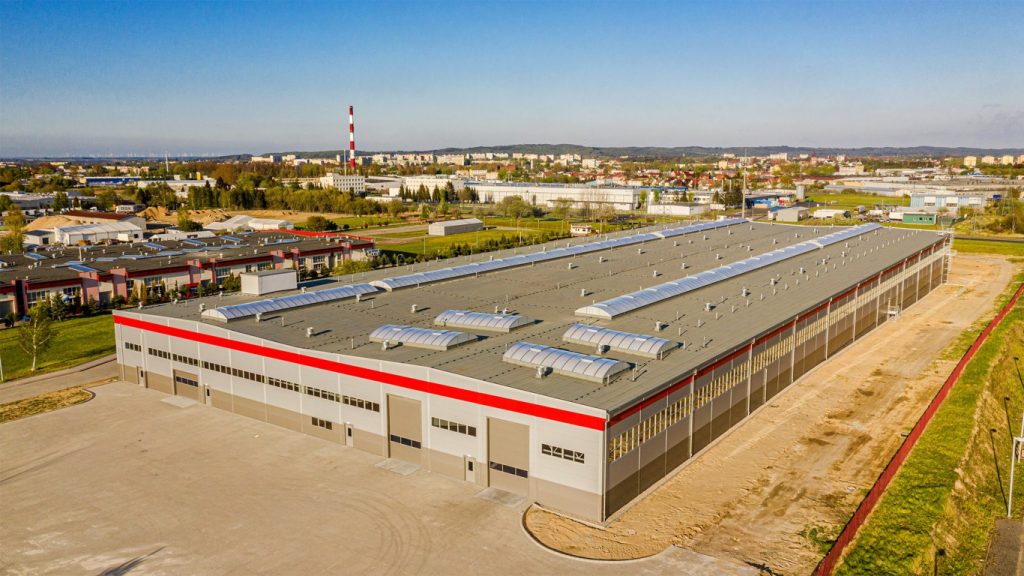
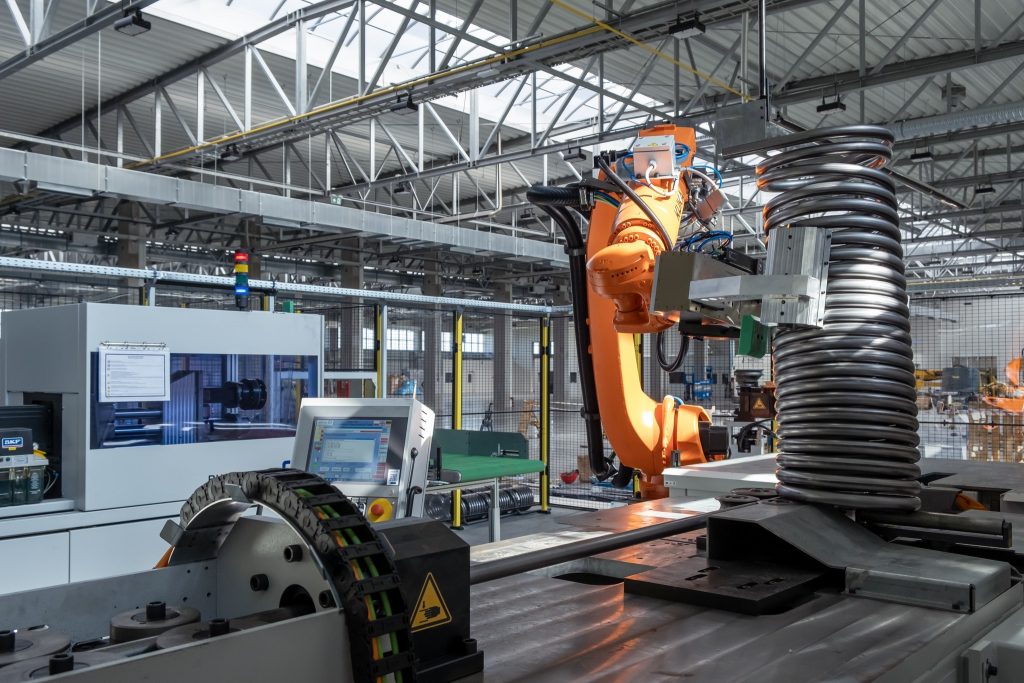
Welding Line – Perfection in Every Joint
Our automated welding line encompasses the entire production process of the jacket – from rolling, bending, welding, through coil assembly, to circumferential and cylinder element welding. All this is done using automatic welding machines and FANUC robots. The welding line ends with a 100% quality control of the cylinder for tightness, ensuring the reliability and durability of our products.
Enameling Area – Energy Savings and Highest Quality
Fully automated lines in the enameling area utilize innovative technologies, such as high-efficiency spray surface preparation, which surpasses traditional immersion methods with extreme energy savings. Wet enameling ensures precise surface coverage, regardless of their complexity. This allows us to accurately enamel both simple and more advanced cylinders equipped with maximum surface coils, used in configurations with heat pumps.
Foaming Line – Innovation and Efficiency
Our team of engineers has developed an innovative foaming process that guarantees high energy indices while simultaneously reducing energy consumption. The elimination of the need for foaming molds allows for a flexible approach to the production process and increases its efficiency.
Packaging Line – Optimization at the Highest Level
Our packaging line, developed by Kospel engineering team, uses Lean tools to maximize the efficiency of packaging processes. This ensures our products are ready for shipment in the shortest possible time, resulting in faster deliveries to our customers.
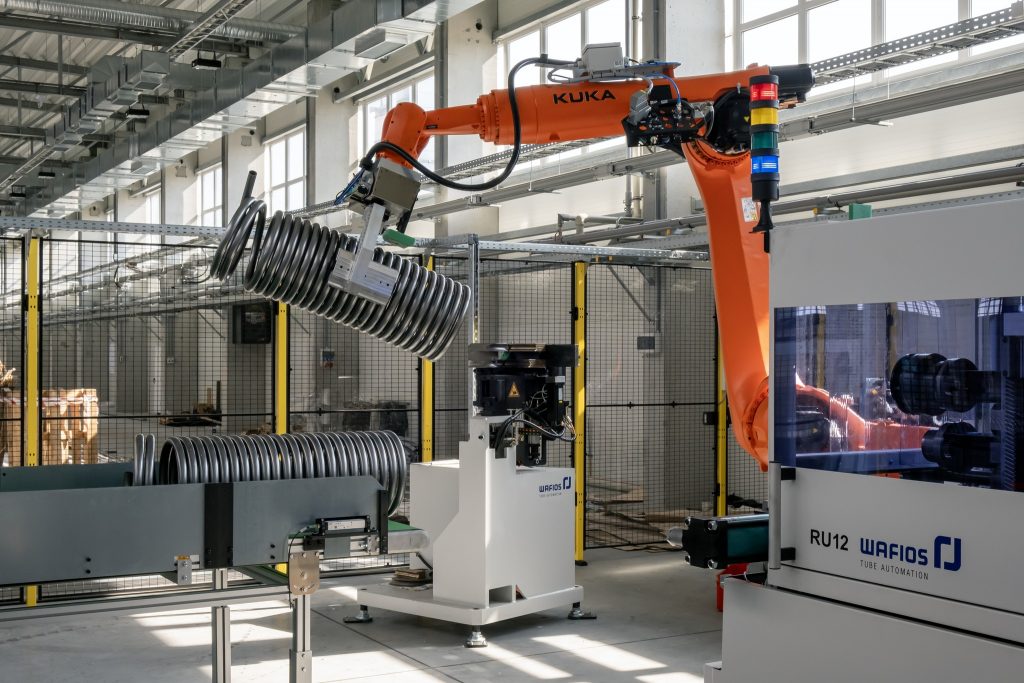
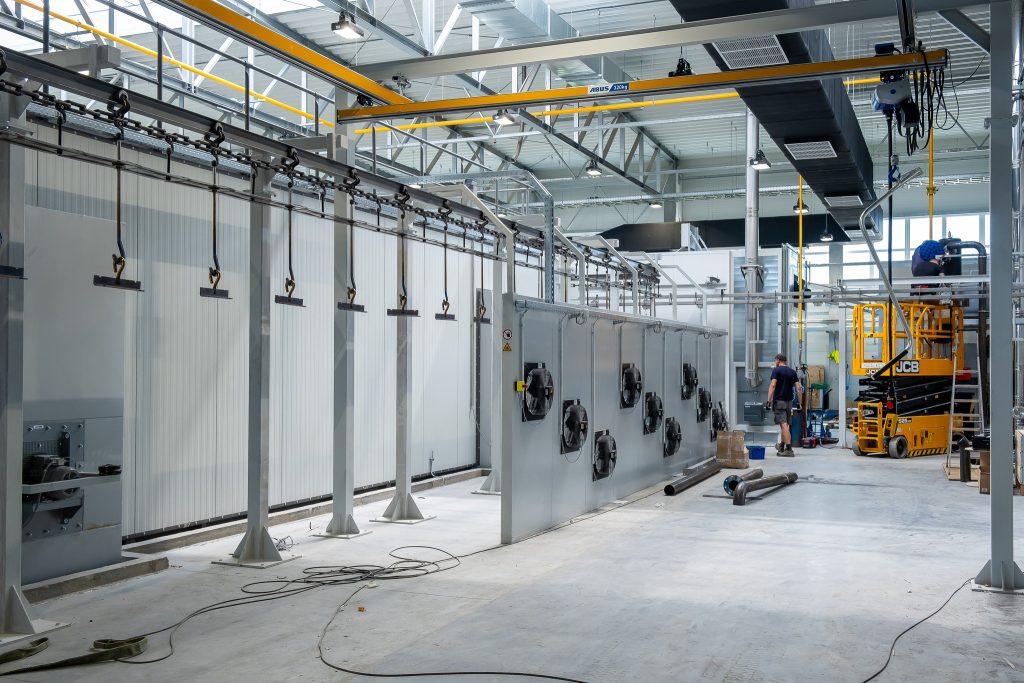
Wastewater Treatment Plant – Ecology First
In the new factory, Kospel utilizes modern industrial wastewater treatment technology based on a vacuum distillation system with recirculation. This results in 98% pure distillate from 100% of the wastewater, which we reuse in our production processes. This is not only a resource-saving measure but also a valuable contribution to protecting our environment.
Expansion of Production Capabilities
Upon launching the new factory, our production capacity will increase by an impressive 300,000 tanks annually. This is a significant step forward, allowing us to better meet the growing market demands and fulfill our customers’ expectations.
The construction of the new, most advanced factory in Europe is an investment in the future of Kospel and our customers. With the advanced technologies we are implementing, we are raising the standards of quality, efficiency, and ecology to a whole new level. We are confident that the new factory will benefit not only us but also our partners and customers by offering products that meet the highest market standards.